Industry Trends4 min
Resilient Construction: How To Make Your Builds More Weather-Resistant
You may have recently heard the terms “resilient construction” or “weather-resistant building” being used more frequently within the architectural and construction industries. But what do these terms mean exactly? The Resilient Design Institute defines resilient construction (or resiliency) as “the capacity to adapt to changing conditions and to maintain or regain functionality and vitality in the face of stress or disturbance.”
A big reason why resiliency has become a movement in the building industry is due to an increase in extreme and unanticipated weather conditions. NASA reports that within recent years sea levels have significantly risen, global temperatures have risen, and ice sheets have been melting at an unusually rapid pace—all of which may be contributing factors to changing weather patterns.
What Resilient Construction Means For The Building Industry
With the increased frequency and severity of weather-related events, there is a new sense of urgency in the building industry. “Weather-resistant building is something everyone should be concerned about, regardless of what region they live in,” advises Mark LaLiberte of Construction Instruction. “It’s time for us all to adapt to a new era of rising consumer expectations.”
Some builders have already stepped up their efforts, delivering homes designed to take on ever-greater blows from Mother Nature—though their methodologies often differ_._ The Washington Post spoke with a number of builders about the importance of weather-resistant building. According to the article, “There is no one-size-fits-all approach to creating a resilient home—solutions vary from region to region.” Although there might be different approaches to resilient construction based on environmental needs—like wind zones, extreme heat and flooding—having the proper building materials can be a crucial factor for mitigating home damage.
Defend Your Build®
LP Building Solutions has recently begun taking a more comprehensive approach to its resiliency efforts by grouping a number of its products under the umbrella of LP Structural Solutions. These products include LP WeatherLogic® Air & Water Barrier, LP® FlameBlock® Fire-Rated Sheathing, LP Legacy® Premium Sub-Flooring and LP® TechShield® Radiant Barrier. This comprehensive portfolio was introduced using the slogan “Defend Your Build”—a statement meant to empower builders and change the way they think about their resilient construction efforts.
"For us, the idea is to get builders to look at their projects holistically," says Jeff Yelle, Director, OSB/EWP Technology at LP Building Solutions. "While each of our products is designed to protect a home from a very specific threat, they can perform even better together as a suite of complementary, high-quality products."
Standing Up To The Elements
Each product in the LP Structural Solutions portfolio has been developed to overcome specific challenges faced by builders under a varied set of conditions. "If you take LP TechShield Radiant Barrier, for example," says Yelle, "it's designed to go beyond what you would expect from a roof sheathing and deliver an added benefit to the structure and homeowner for years to come. Then we looked at what else we could do that would produce additional value and resiliency." The same approach informed the development of other products in the LP Structural Solutions portfolio-whether it's LP FlameBlock Fire-Rated Sheathing or the moisture management technology used in LP WeatherLogic panels, which offer a continuous air and water barrier for a tight building envelope while allowing moisture to escape.
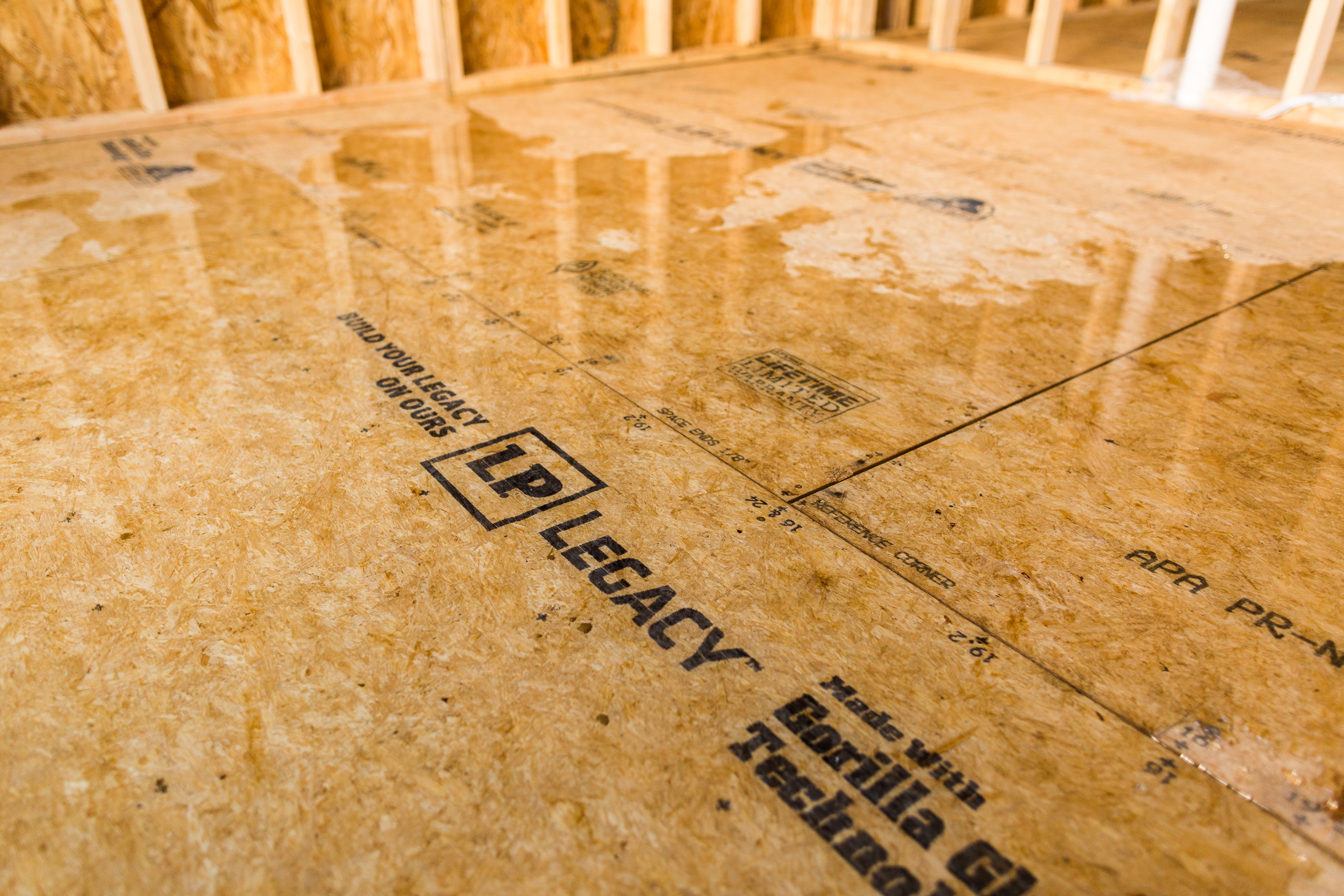
"It's all about providing solutions to problems," Yelle explains. "For instance, if the LP Legacy panels get rained on during installation, they don't have to be re-sanded-and that's a very practical jobsite benefit that any builder can appreciate."
Outside of the LP Structural Solutions portfolio, there are other offerings from LP that can aid builders in their resilient building efforts. Our LP® SmartSide® Trim & Siding and LP SolidStart products also meet additional resiliency needs as they are manufactured to withstand harsh elements and offer some impact resistance.
Builders Must Adapt
While LP's products are a valuable resource for builders looking to construct high-performance, weather-resistant buildings, ultimately other factors will also come into play. Simply put, builders will have to adapt to the elevated expectations in the marketplace. This may mean increasing standards in the installation process itself. "Accuracy will be more important than ever to assure the best possible performance," predicts Yelle.
As Mark LaLiberte points out: "Homeowners are expecting change. They are expecting higher quality products that will protect their homes. And it is up to the builders to rise to the occasion and build in these improvements which lower risk and improve customer satisfaction."
Subscribe to our newsletter for updates on climate resistant industry trends and more!
Continue Reading
Resiliency Solutions
5 minIntroducing LP® SmartSide® ExpertFinish® Naturals Collection™: Nature-Inspired Beauty Meets Engineered Performance
We’re excited to introduce the LP® SmartSide® ExpertFinish® Naturals Collection™, a bold new addition to our trusted line of engineered wood siding and trim that delivers the warmth and beauty of nature with the advanced protection and performance builders and homeowners expect.
Labor Solutions
5 minChoosing the Right LP® Structural Solutions Product for Your Build
When it comes to building strong, reliable, and high-performing structures, the materials you choose matter. At LP Building Solutions, we understand that every project, whether it's a single-family home or a multifamily development, requires structural components that meet your needs for strength, durability, and efficiency.
Sustainability Solutions
5 minBuilding a More Sustainable Future with LP Building Solutions
In today's world, sustainability is no longer just a buzzword, it's a blueprint for responsible living and smarter building. As the construction industry seeks ways to reduce its environmental footprint, LP Building Solutions is focused on providing innovative building materials for eco-conscious builders to help reshape what it means to build sustainably
News & Stories3 min
History of Partnership with Gary Sinise Foundation
The LP Foundation is a proud partner of the Gary Sinise Foundation, which supports wounded veterans in several ways. You can learn more about the LP Foundation here.