Business Advice6 min
Adapting to Building Codes: How LP Structural Solutions Can Help Builders Succeed
The first building code in the U.S. was in 1625, addressing fire safety for roof coverings. In 1630, building codes in Boston outlawed wood chimneys and thatch roofs. And in the 1770s, following a recommendation from George Washington, building codes in Washington, D.C. imposed height restrictions on wood-frame buildings. In the 250 years since, states, counties and other municipalities have adopted a variety of building codes, challenging builders to quickly adapt their construction practices.
What are some of the more specific building codes the U.S.? And how do U.S. climate zones reflect those codes? We spoke with Neil Freidberg, Building Science Manager at LP Building Solutions, to learn how to adapt to building codes and how LP Structural Solutions can help.
Challenges in Adapting to Building Codes
When it comes to how often building codes are updated, the process involves production, review and final approval. Across the U.S., individual states adopt the International Building Code or International Residential Code (IRC) for single-family construction rules with adaptations. "Codes are updated every three years, and then states can choose to adopt the code that is released," says Freidberg. "Local municipalities can also choose to make their codes stricter or looser."
That's one of the reasons why it's so difficult for builders to expand into new areas of the country. It takes tremendous time and effort for builders to understand the local building codes.
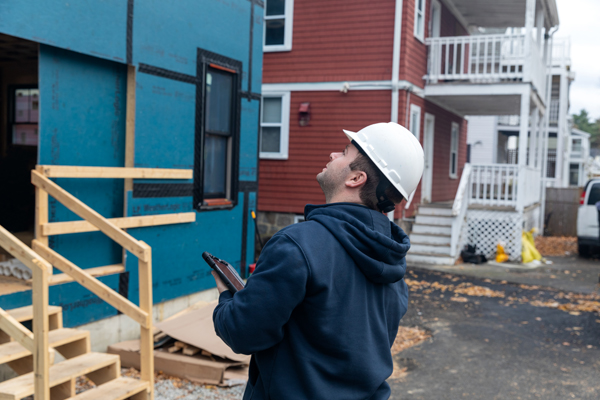
So how do you adapt to the building codes in the area?
State building codes use climate maps like IECC climate and ASHRAE climate zone maps to calculate minimum design and construction requirements to help ensure safe and resilient structures. Establishing building codes specific to the climate zone often creates highly specific codes, but they work to build stronger buildings that can withstand local potential disasters.
"Two things drive code," says Freidberg. "One is the overwhelming requirement to be more energy efficient. And two are high-failure events like fire, earthquakes, tornadoes or hurricanes impacting the community."
If several buildings collapse following a high-wind event, for example, the government will investigate. The learnings can then lead to recommendations to better brace for future weather events, Freidberg explains.
“Sometimes they find structures were not built strong enough, leading to changes in future editions of the code,” says Freidberg.
Examples of Specific Codes and How LP Structural Solutions Can Help
When cities have code requirements specific to their climate zones, the LP Structural Solutions portfolio can often help builders meet code requirements. Let's review a few examples:
Codes on High Wind. A majority of the Atlantic coastal region—from Maine to Florida—has distinct building codes to add greater resiliency against hurricane-force winds. Since high wind can create substantial horizontal loads on a structure, many areas require shear walls to help transfer those loads down to the foundation.
Classified as Structural I sheathing, LP WeatherLogic® Air & Water Barrier panels boast added structural strength for both walls and roofs. The WRB membrane added to the OSB sheathing provides moisture resistance which, with all panels joints properly taped or sealed, helps make it a complete water-resistive barrier for moisture management.
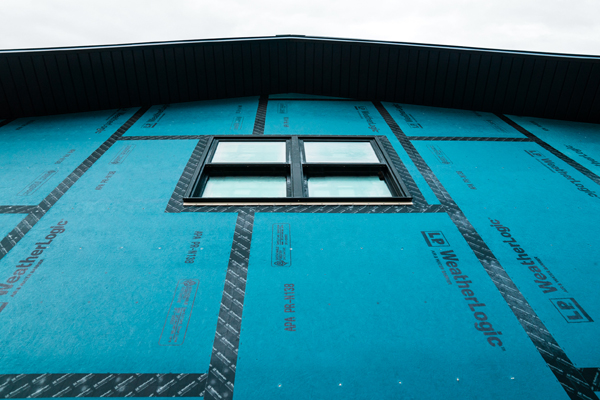
Check out this case study from Galveston, Texas, and read more about how builders can balance resilient design with building codes in hurricane zones.
Codes on Ignition-Resistance. Wildlife-urban interface (WUI) areas also require specific codes due to their specific climate zones and needs. When constructing buildings in areas that require ignition-resistant construction, turn to LP® FlameBlock® Fire-Rated Sheathing, which combines flame-spread and burn-through resistance to help meet code requirements for ignition-resistant construction. The fire-rated sheathing, which can be used on walls and roof decks, features a proprietary non-combustible, fiberglass-reinforced Pyrotite® coating.
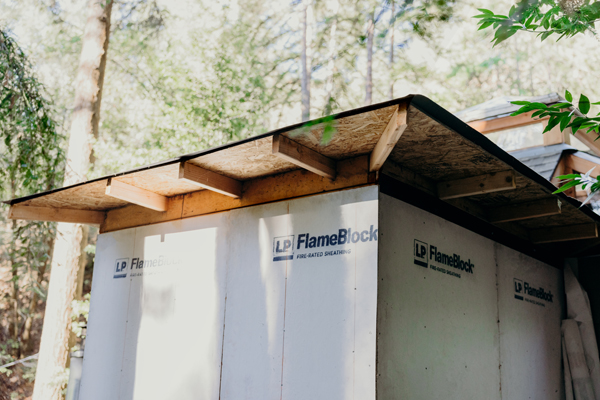
Working with LP on Your Code-Compliant Builds
"LP is constantly challenged by code because we're always looking for the right thing to do," says Freidberg. He explains that's just one of the reasons LP works closely with investigating agencies and organizations and keeps an eye on how climate changes are impacting our communities.
Continue Reading
Resiliency Solutions
5 minIntroducing LP® SmartSide® ExpertFinish® Naturals Collection™: Nature-Inspired Beauty Meets Engineered Performance
We’re excited to introduce the LP® SmartSide® ExpertFinish® Naturals Collection™, a bold new addition to our trusted line of engineered wood siding and trim that delivers the warmth and beauty of nature with the advanced protection and performance builders and homeowners expect.
Labor Solutions
5 minChoosing the Right LP® Structural Solutions Product for Your Build
When it comes to building strong, reliable, and high-performing structures, the materials you choose matter. At LP Building Solutions, we understand that every project, whether it's a single-family home or a multifamily development, requires structural components that meet your needs for strength, durability, and efficiency.
Sustainability Solutions
5 minBuilding a More Sustainable Future with LP Building Solutions
In today's world, sustainability is no longer just a buzzword, it's a blueprint for responsible living and smarter building. As the construction industry seeks ways to reduce its environmental footprint, LP Building Solutions is focused on providing innovative building materials for eco-conscious builders to help reshape what it means to build sustainably
News & Stories3 min
History of Partnership with Gary Sinise Foundation
The LP Foundation is a proud partner of the Gary Sinise Foundation, which supports wounded veterans in several ways. You can learn more about the LP Foundation here.